Manufacturing Costs: Significance, Types, and Cost Calculation
Last updated on: October 27, 2023
Wondering how manufacturing companies determine their costs and ensure they stay profitable?
Whether you’re just starting your own manufacturing business or are looking to venture into the field of cost accounting, understanding manufacturing costs and knowing how to accurately calculate them is crucial for success.
In this comprehensive guide, we will explain what manufacturing costs are and delve into:
- The different types of manufacturing costs,
- The step-by-step process of calculating them,
- Examples of manufacturing costs, and
- The benefits of calculating manufacturing costs.
Let’s get started.
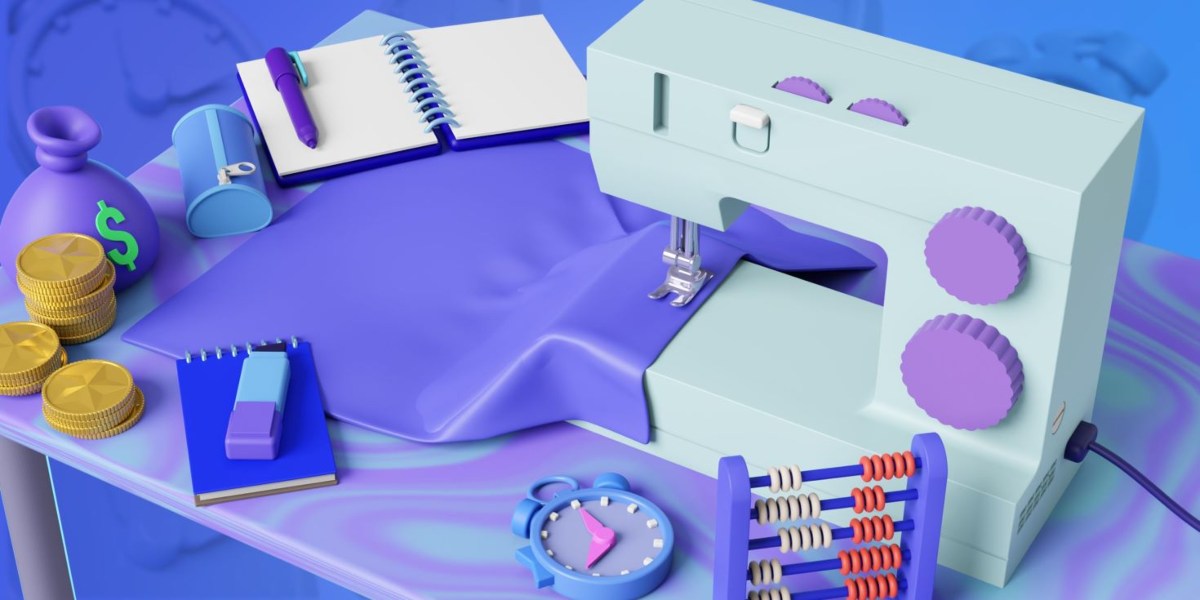
Table of Contents
What are manufacturing costs?
Manufacturing costs, also called product costs, are the expenses a company incurs in the process of manufacturing products.
Manufacturing costs include:
- Direct costs and
- Indirect costs.
Accurate cost calculation helps companies identify the processes or materials that are driving up manufacturing costs and determine the right pricing of products — the keys to remaining profitable.
That’s not all.
According to McKinsey’s research, cutting down manufacturing costs, in addition to boosting productivity, is the key for manufacturing companies to remain competitive.
Now, let’s explore both types of costs in more detail.
What are direct manufacturing costs?
Direct manufacturing costs are expenses that can be attributed directly to the production of a specific product. They include costs related to:
- Direct materials: these are the tangible inputs (or raw materials) used in the manufacturing process. For instance, the cost of the screen and electronic components would be considered direct material costs if these materials are readily traceable to the finished product (for example, glass used to make light bulbs).
- Direct labor: this involves the wages and benefits paid to workers who are directly involved in assembling or creating the product, such as welders, assemblers, and machine operators. For example, the wages of assembly line workers working on the smartphone production line fall under direct labor costs. In addition to basic wages, direct labor costs will also include overtime pay, payroll taxes, and benefits (health insurance, workers’ compensation, retirement plans, and contributions to social security or pension funds).
- Expenses directly linked to the manufacturing process or the manufactured product: costs associated with the use of utilities like electricity, water, and natural gas that are directly tied to the production process also qualify as direct costs.
What other costs should you include when computing the cost of direct materials?
According to Zaher Dehni, EA-certified tax professional at Taxfully, you will also need to consider:
- The procurement price of raw materials (the cost involved in finding suppliers, storing raw materials, and so on),
- The cost of shipping the raw materials to the production site, and
- Any pertinent duties (a form of tax) associated with importing raw materials.
When you add up all these direct costs, you get the Cost Of Goods Sold (COGS), a term used in accounting when preparing the company’s financial statement.
What are indirect manufacturing costs?
Indirect manufacturing costs include all other expenses incurred in manufacturing a product except direct expenses.
These indirect costs, also called factory or manufacturing overheads, include costs related to property tax, insurance, maintenance, and other indirect operations that support the production process.
According to a study conducted by McKinsey, these indirect costs account for 8% to 12% of the overall manufacturing costs.
Now that you are familiar with the components that constitute manufacturing costs, let’s move on to the process of calculating these expenses.
How to calculate total manufacturing cost?
Calculating the total manufacturing cost involves calculating the costs of:
- Direct materials,
- Direct labor,
- Other direct expenses, and
- Factory overheads.
Here is the simple formula to calculate the overall manufacturing cost:
Manufacturing cost = the cost of direct materials + direct labor + other direct expenses + factory overhead (manufacturing overheads)
Let’s go through all the steps for calculating total manufacturing costs.
Step #1: Calculate the cost of direct materials
To calculate the cost of direct materials you need to know the cost of inventory. Let’s see how to find out the value of inventory.
First, collect cost information. Start by making a list of all the direct materials that are used to make the specific product and obtain the cost information for the direct materials you have identified.
Next, calculate the value of the existing inventory if the manufacturing company already has a stock of materials from a previous period.
Then, add up the cost of new inventory — this is the cost of raw materials you purchase to manufacture the product.
Now, add the value of existing inventory to the cost of purchasing new inventory to calculate the cost of direct materials.
From this, subtract the remaining inventory after manufacturing the product. This gives you the value of direct materials used, according to M.C. Shukla, the author of Cost Accounting: Texts And Problems.
For instance, let’s say a company has an existing inventory worth $1,500.
The company purchases $1,000 worth of new materials to make product X.
Now, the total inventory value is:
$1,500 + $1,000 = $2,500
After manufacturing product X, let’s say the company’s ending inventory (inventory left over) is $500.
This means, the cost of direct materials is:
$2,500 – $500 = $2,000
Step #2: Compute the cost of direct labor
To calculate the direct labor cost, you will need to know the following:
- The total number of employees working on the production line,
- The total number of hours each employee works, and
- The hourly rate of labor.
To obtain these details, you can refer to the company’s employment records that has a list of all the employees and their hourly rates.
Tracking the number of hours each employee works on the production line can be tricky. This is where a manufacturing time tracking app, such as Clockify, comes in handy.
With Clockify, workers can quickly clock in and clock out.
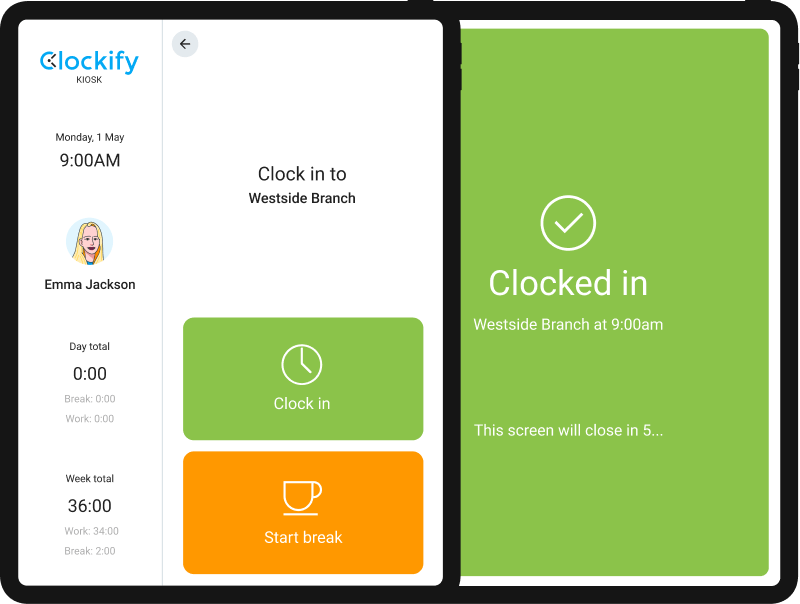
As employees use Clockify to clock in and out, employers gain insights into the total number of hours each employee worked on each production line. You can also see the total number of hours worked by the entire team.
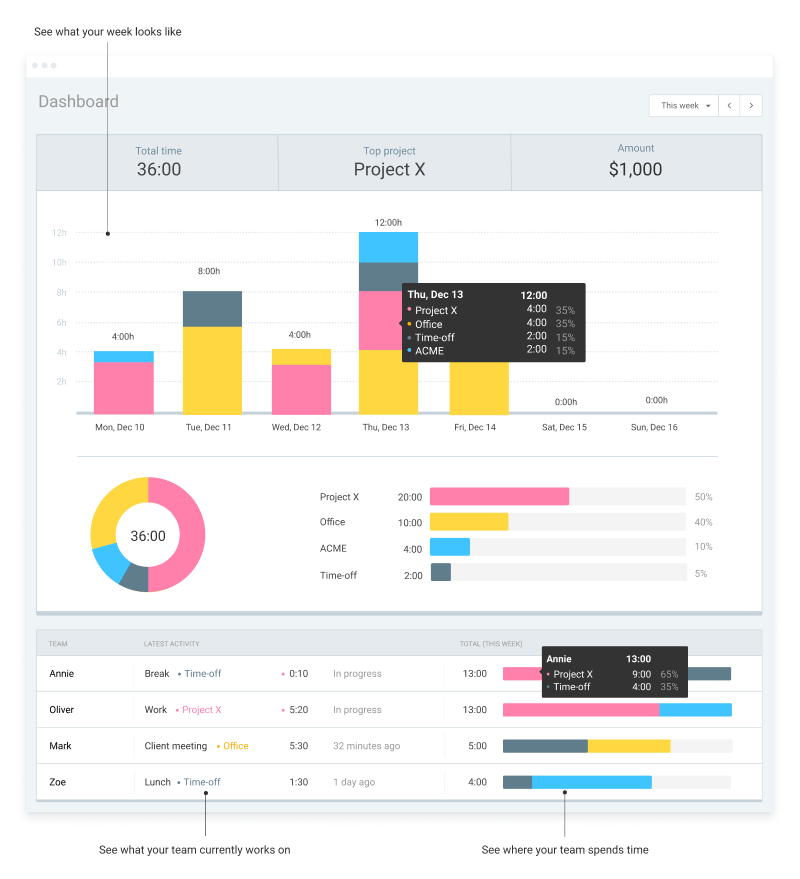
Once you know the number of hours worked by employees, you can calculate the cost of direct labor with this formula:
Direct labor = Hourly labor rate / the total number of hours worked on the production line by all employees
For instance, let’s say the hourly rate a manufacturing company pays to its employees is $30.
Here are the number of hours each worker worked:
- Worker 1— 6 hours
- Worker 2 — 7 hours
- Worker 3 — 9 hours
So, the direct labor cost per hour is:
$30 (hourly labor rate) / 22 (total number of hours worked) = $1.36
While this is a simplified view of direct labor calculation, accountants also include the benefits, overtime pay, training costs, and payroll taxes when calculating the hourly rate.
💡 Clockify Pro Tip
Master labor cost calculations with smart tips and easy-to-use calculators. Read our blog post:
Step #3: Add up the other direct expenses
The next step is to calculate the costs of utilities (electricity, water, or gas) that are directly used in the manufacturing process (for example, fuel used to operate the production equipment).
Step #4: Calculate the indirect costs (manufacturing overheads)
To calculate the indirect manufacturing costs you first need to identify all the indirect costs associated with the manufacturing process.
These costs typically fall into categories such as:
- Rent,
- Utilities,
- Depreciation,
- Maintenance,
- Supplies,
- Insurance, and
- Indirect labor (e.g., supervisors and quality control staff).
Once you identify the indirect costs, get detailed expense data for each of these overhead cost categories for a specific period, such as a month or a year. You can track expenses by looking at your invoices, receipts, and records of all expenditures related to manufacturing overhead.
Be sure to allocate overhead costs to the respective cost centers (specific departments, processes, or machines in the manufacturing facility that contribute to the manufacturing costs).
For example, you can allocate depreciation costs of refrigerators to the department that uses them.
Here is the breakdown of overhead costs of company Z that makes smartphones:
Overhead categories | Cost |
---|---|
Indirect materials | $7,000 |
Property tax | $6,000 |
Insurance | $12,000 |
Office rent | $9,000 |
Depreciation | $15,000 |
Maintenance | $10,000 |
Total indirect expenses | $59,000 |
Calculating the overhead cost for manufacturing one unit
While the calculation above gives you the total overhead costs, you will need to calculate the overhead cost for manufacturing one unit by using this formula:
Overhead cost of manufacturing one unit = Total overhead cost / number of units manufactured
For instance, if company Z makes 20,000 smartphones, the overhead cost (total indirect expenses) of manufacturing one smartphone:
$59,000 / 20,000 = $2.95
Knowing the overhead cost per unit is helpful in understanding what the manufacturing overhead costs will be if the company plans to double their production (in other words, make 40,000 smartphones) in the future, for instance.
Step #5: Calculate the total manufacturing cost
The last step is to calculate the total manufacturing cost by adding up all the above components:
- Direct labor,
- Direct materials,
- Other direct expenses, and
- Factory overheads.
You will do that by using the total manufacturing cost formula we mentioned above:
Total manufacturing cost = Direct labor + direct materials + other direct expenses + manufacturing overheads
If this process of calculation looks complex, fret not.
According to Francis Fabrizi, AATQB (The Association of Accounting Technicians Qualified Bookkeeper) at Keirstone Limited, there are specific tools that can help you streamline the calculation process:
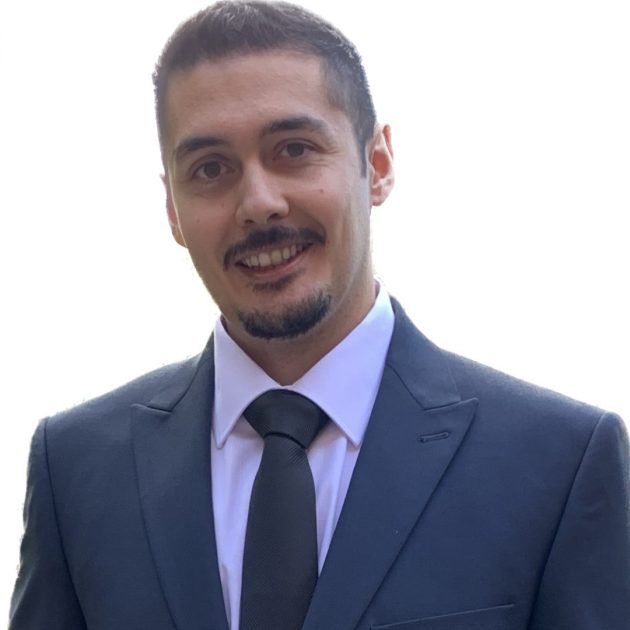
“Some of the most popular options include:
- “Manufacturing ERP (Enterprise Resource Planning) systems that provide a comprehensive set of tools for managing all aspects of the manufacturing process,
- Manufacturing Execution Systems (MES) that offer real-time data on the manufacturing process, and
- Cloud-based cost accounting software which is a cost-effective way to track and manage manufacturing costs.”
The challenges of calculating manufacturing costs
Fabrizi also talked about the common challenges manufacturers face when calculating the costs of production. In his experience, the most common challenges are a lack of accurate data and the complexity of costing methods.
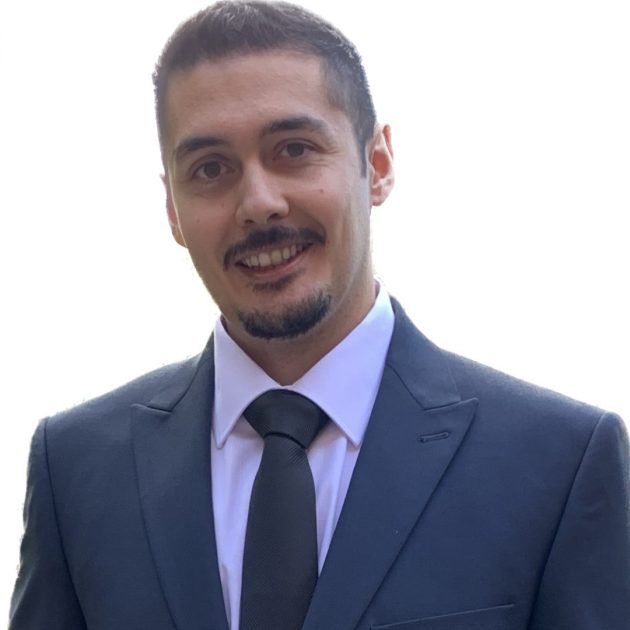
“Lack of accurate data as inaccurate data can lead to incorrect cost calculations, which can have a negative impact on the bottom line. Some costing methods are more complex than others which can prevent them from tracking and managing costs, making it difficult to get a clear picture of all of the costs involved in the manufacturing process.”
Fluctuation of costs is yet another challenge that makes it harder to calculate manufacturing costs accurately, according to Fabrizi.
What are examples of manufacturing costs?
Manufacturing costs are typically grouped under three categories:
- Direct materials,
- Direct labor, and
- Manufacturing overhead.
Let’s look at them in more detail.
Example #1: Direct materials
Here are some examples of direct materials that contribute to manufacturing costs:
- Raw materials: these are the materials used in the production process. Raw materials become part of the finished product, such as wood used to make furniture, steel to manufacture appliances, or plastic used to make toys.
- Components: the cost of the individual components and semi-finished goods that are assembled to create the final product. For example, some car manufacturers buy individual components, such as car engines from other companies and assemble them. Semi-finished goods are those that have undergone some initial manufacturing steps but are not considered final products. An example is the fabric that has been cut and partially sewn into garment pieces but is not a complete piece of clothing yet.
- Packaging materials: the cost of materials used for packaging the finished product, such as boxes, labels, and other packaging materials.
Example #2: Direct labor
Direct labor costs include the wages and benefits paid to employees directly involved in the production process of goods or products.
Here are some examples of the different types of employees whose wages and benefits come under the category of direct labor costs:
- Assembly line workers: these are the employees who work on assembly lines, putting together various components to create the final product. For example, in an automobile manufacturing plant, assembly line workers are responsible for assembling different parts of a car.
- Machine operators: workers who operate machinery and equipment used in the manufacturing process. For instance, in a textile factory, machine operators oversee the operation of weaving machines or looms.
- Welders: skilled workers responsible for joining metal parts together through welding processes.
- Painters and finishers: workers responsible for applying paint, coatings, or finishes to products, such as furniture or metal components.
- Electricians and technicians: skilled technicians who install, maintain, and repair electrical systems and equipment used in manufacturing processes.
Example #3: Other direct costs
These are the expenses that are directly tied to the production of goods but may not fall into the categories of direct materials or direct labor. Here are some examples of other direct costs in manufacturing:
- Energy costs: these include the costs of electricity, natural gas, and other forms of energy used to power machinery and equipment during the manufacturing process. For example, the electricity used to run machines in a steel mill.
- Tooling and setup costs: costs related to the setup of machinery and equipment for specific production runs, including the cost of tooling, fixtures, and molds.
- Subcontractor costs: manufacturing companies often outsource certain aspects of production or certain components to other companies. The fees paid to these subcontractors are examples of direct manufacturing costs. For example, an automotive manufacturer can outsource the production of car seats to another company.
Example #4: Indirect manufacturing costs (factory overheads)
Here are some examples of indirect manufacturing costs:
- Factory rent: the cost of renting the manufacturing facility where production takes place is an example of an indirect manufacturing cost.
- Utilities: expenses related to electricity, water, heating, and cooling used in the administrative office are considered indirect manufacturing costs.
- Depreciation: the reduction in value of manufacturing equipment over time is a form of indirect manufacturing cost.
- Taxes: indirect manufacturing costs will include the taxes that companies pay on the commercial property they use for manufacturing. Taxes will also apply to any equipment, machinery, computers, furniture, and tools used to manufacture the product.
- Insurance: manufacturers need to buy several types of insurance policies to protect themselves from risks, such as property damage, employee accidents or injuries, equipment breakdown, customer liability, and natural disasters.
- Fuel: the cost of fuel used in office cars or other forms of transportation is also counted as indirect cost.
- Indirect labor: a manufacturing unit typically involves many employees who are not directly involved in the manufacturing process but support the process indirectly. The wages paid to these employees will also come under factory overheads. Examples include supervisors, administrators, accountants, and human resources.
- Indirect operations: there are many activities that do not directly involve physically transforming raw materials into the finished products but support the production process. Examples include maintenance, quality control, supply chain management, research and development, and so on.
💡 Clockify Pro Tip
Learn the cost of quality and stop quality issues in their track with this insightful blog post:
What are the benefits of calculating manufacturing cost?
According to the book Manufacturing Cost Estimating, the benefits of calculating the costs of manufacturing range from guiding investment decisions to cost control. Let’s take a closer look at these benefits.
Benefit #1: Assists in cost control
Cost control, according to Fabrizi, is one of the top benefits of calculating manufacturing costs.
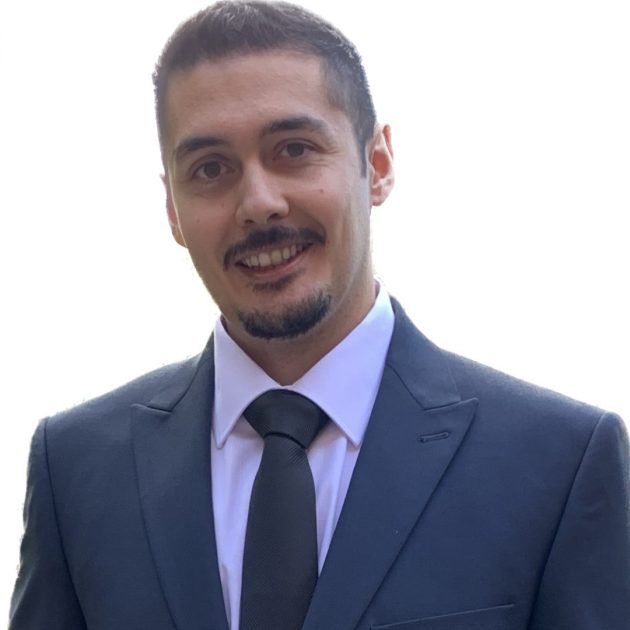
“By tracking and monitoring costs, manufacturers can stay on top of their costs and avoid unexpected expenses.”
By calculating manufacturing costs, manufacturers can better understand the elements that are driving up costs while identifying the most economical way to manufacture a product.
For instance, if some raw materials are driving up costs, manufacturers can negotiate with other suppliers who may be willing to supply these materials at a lower cost.
Here’s an interesting case study on how manufacturing cost analysis helped a steel manufacturing company save costs.
The company engaged a consulting firm to help them find out what factors were driving up manufacturing costs. By looking at the historic data on employee timesheets and purchasing costs, the firm was able to understand the areas that were increasing the total manufacturing costs.
The consulting firm was also able to re-negotiate the manufacturing company’s contracts with poor-performing suppliers.
As a result, the steel manufacturing company was able to achieve a 10% reduction in manufacturing costs and save €1 million (approximately $1.7 million) annually.
Benefit #2: Helps make informed pricing strategies to stay competitive
By calculating manufacturing costs, companies can clearly understand the true cost of making a product. Based on this information, the company’s management can add a markup to determine competitive selling prices for their products.
For instance, Ford Motor Company has reduced the price of F-150 Lightning, its electric car, by $10,000. The company has been able to do so by consistently working on improving the efficiency of production and lowering manufacturing costs. For that purpose, the company used sensors to collect and analyze the cost of materials in real time to see how to optimize the costs.
As you can see, by collecting cost data and calculating it accurately, businesses can optimize cost management and set the right price for their products to gain a competitive advantage.
Benefit #3: Assess the profitability of a product
Calculating manufacturing costs helps assess whether producing the product is going to be profitable for the company given the existing pricing strategy.
According to a study titled The Impact of Cost Control on Manufacturing Industries’ Profitability, businesses can boost their profitability by controlling the costs related to:
- Labor,
- Materials, and
- Overheads.
Manufacturing cost calculation gives an accurate view of the costs allowing companies to eliminate irrelevant costs and optimize resource utilization to boost profitability.
💡 Clockify Pro Tip
Want to know how time tracking helps you maximize your earnings on every project? Check out our Clockify help article:
Benefit #4: Assists in “make or buy” decisions
With a breakup of all the costs of manufacturing, management can decide whether it is more profitable to purchase certain parts or materials from a vendor or manufacture them in-house.
As an illustration, let’s look at the findings of a case study titled Saving the Company with Contract Manufacturing.
A manufacturing company initially purchased individual components from different vendors and assembled them in-house. As the company decided to assemble the components themselves, they found that the costs of managing the assembly line and the transportation were increasing significantly.
As a result, the company decided to outsource production to a contract manufacturing company (a company that enters into a contract with the manufacturer to make certain components) instead of assembling components in-house. This resulted in a 30% reduction in manufacturing costs.
The key takeaway of this case study is that understanding the fluctuations in manufacturing costs can empower companies to make informed and timely choices between outsourcing and in-house production. These informed decisions help in maximizing productivity and profitability.
Benefit #5: Guides investment decisions
Manufacturers can compare the costs of making a product using different manufacturing processes. This helps them understand the most efficient process and the investment they need to make for the selected process.
For instance, if the manufacturing costs are too high, these costs can create a dent in the company’s profit. In this case, the management can decide to stop the production of some goods and invest in developing new ones that have a lower cost of production.
FAQs about manufacturing costs
Have more questions on manufacturing costs? We’re here to help. Here are some frequently asked questions (FAQs) and answers that address key concepts related to manufacturing costs.
What are material costs in manufacturing?
Material costs are the costs of raw materials used in manufacturing the product. These materials become part of the finished product.
What are manufacturing costs also known as?
Another commonly used term for manufacturing costs is product costs, which also refer to the costs of manufacturing a product.
Is manufacturing cost an asset?
Yes. Manufacturing costs are recorded as assets (or inventory) in the company’s balance sheet until the finished goods are sold.
Wondering what assets and balance sheets mean?
A balance sheet is one of the financial statements that gives a view of the company’s financial position, while assets are the resources a company owns. These assets have value and the company can sell them to earn revenue.
As the manufacturing process involves raw materials and finished goods, all of these are considered assets. The materials that are yet to be assembled /processed and sold are considered work-in-process or work-in-progress (WIP) inventory.
WIP inventory is the sum of the cost of labor, raw materials, and overhead costs involved in manufacturing the product. Francis Fabrizi explains that the goods that are waiting to be sold are recorded as assets and once they are sold, they are recorded as expenses:
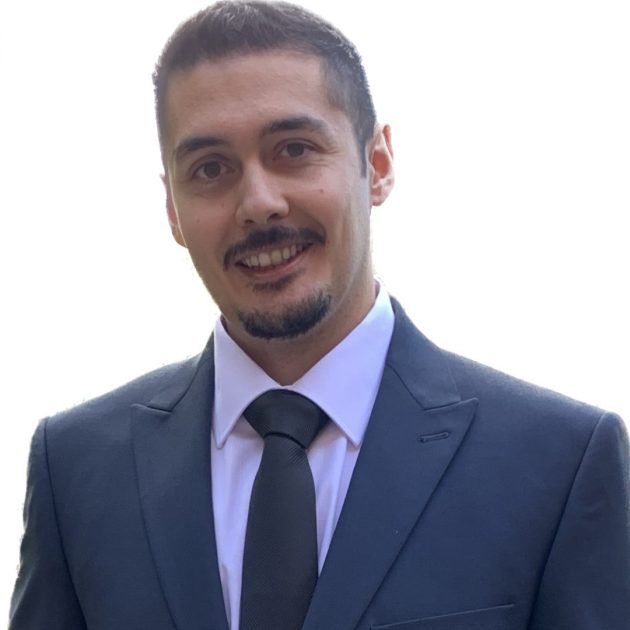
“When a manufacturer begins the production process, the costs incurred to create the products are initially recorded as assets in the form of WIP inventory.
When the finished products are sold, the manufacturing costs are no longer considered assets. Instead, they are transferred from the inventory account to the Cost of Goods Sold (COGS) account on the income statement.”
To sum up, finished goods that are not yet sold are considered assets.
What is manufacturing cost vs. non-manufacturing cost?
Manufacturing costs are directly associated with the production of goods. On the other hand, non-manufacturing costs are expenses incurred outside of the production process, such as:
- Marketing,
- Sales, and
- Administrative expenses.
What factors are related to manufacturing costs?
Many factors can influence manufacturing costs, such as:
- Production volume,
- Labor costs,
- The skill level and efficiency of labor,
- Equipment efficiency,
- Raw material prices, and
- Overhead costs.
Conclusion: Take a step-by-step approach to calculating manufacturing costs
To sum up, manufacturing costs include a wide range of expenses, from direct materials and direct labor to indirect manufacturing costs.
These costs play a central role in determining product pricing, assessing profitability, and making strategic “make or buy” decisions.
By diligently calculating and managing manufacturing costs, companies can enhance cost efficiency, maintain competitiveness, and improve their bottom line.
We hope that the detailed explanations, examples, and FAQs provided here have shed light on the complexities of manufacturing costs and will serve as valuable resources for businesses in the manufacturing sector.
✉️ What steps do you follow to calculate manufacturing costs? Feel free to share your insights with us at blogfeedback@clockify.me and we will feature them in our future posts. If you found our blog post informative, go ahead and share it with your coworkers, associates, and industry contacts.